A plane wall of a furnace is fabricated – The fabrication of plane walls in furnaces is a critical aspect of furnace design, influencing factors such as thermal efficiency and heat transfer. This article delves into the materials, design considerations, heat transfer analysis, and applications of plane walls in furnace systems, providing a comprehensive overview for engineers and researchers.
Plane walls, integral components of furnaces, are designed to withstand high temperatures and facilitate efficient heat transfer. Understanding the principles governing their fabrication and performance is essential for optimizing furnace operations and enhancing thermal efficiency.
1. Fabricated Plane Wall of a Furnace
A plane wall in a furnace serves as a crucial component that separates the combustion chamber from the surrounding environment. Its primary purpose is to minimize heat loss from the furnace while maintaining the desired temperature within the combustion zone.
Plane walls are typically fabricated using materials with high thermal resistance, such as refractory bricks, ceramics, or insulating materials. The thickness of the plane wall is determined by various factors, including the operating temperature of the furnace, the desired thermal efficiency, and the available space.
2. Design Considerations
The design of a plane wall involves several key considerations:
- Thermal Conductivity:The thermal conductivity of the wall material plays a vital role in determining the heat transfer rate. Higher thermal conductivity materials result in increased heat loss.
- Heat Transfer Coefficient:The heat transfer coefficient at the surface of the wall influences the rate of heat transfer between the furnace and the surroundings.
3. Heat Transfer Analysis
Heat transfer in a plane wall can occur through three modes: conduction, convection, and radiation. Fourier’s law is commonly used to analyze heat transfer in such walls, which describes the heat flux as proportional to the temperature gradient.
By applying Fourier’s law, engineers can determine the temperature distribution within the plane wall and estimate the heat loss.
4. Thermal Efficiency, A plane wall of a furnace is fabricated
The thermal efficiency of a plane wall is a measure of its ability to retain heat within the furnace. Factors affecting thermal efficiency include:
- Wall thickness
- Material thermal conductivity
- Heat transfer coefficients
To improve thermal efficiency, engineers can increase the wall thickness, use materials with lower thermal conductivity, or enhance the heat transfer coefficient.
5. Applications
Plane walls are extensively used in various furnace applications, including:
- Industrial furnaces for heat treatment
- Boilers for steam generation
- Incinerators for waste disposal
By optimizing the design and materials of plane walls, engineers can improve the overall performance and efficiency of furnaces, reducing energy consumption and operating costs.
FAQ Explained: A Plane Wall Of A Furnace Is Fabricated
What are the key factors to consider when designing a plane wall for a furnace?
The thickness, thermal conductivity, and heat transfer coefficient are critical factors that influence the design of a plane wall for a furnace.
How does thermal conductivity affect the performance of a plane wall?
Thermal conductivity is a measure of a material’s ability to transfer heat. Higher thermal conductivity materials facilitate more efficient heat transfer through the plane wall.
What are the common applications of plane walls in furnaces?
Plane walls are widely used in furnaces for heat treatment, combustion processes, and industrial heating applications.
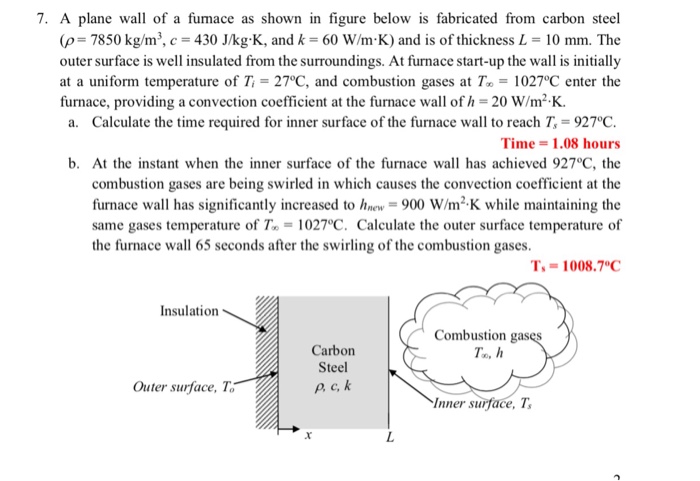
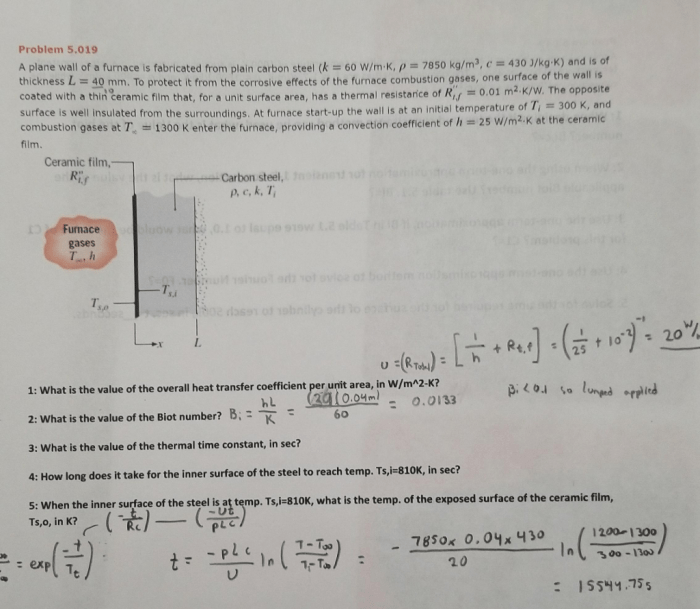